Video documentation
DEVELOPMENTS OF THE EURO-K
The Dual Fuel Use method of Euro-K GmbH makes it possible to burn liquid and gaseous fuels simultaneously and parallelly. Innovative burner designs in conjunction with automated fuel systems concludes a wide range of fuel-flexibility, equipped with the Dual Fuel System application. Hereby, the fuel conversion can be put into effect completely during the operation without interrupting the power output. Thus, the applications can be adapted to different infrastructure boundary conditions without time loss (conversion).
Further developments of our house
The productivity and thus also the efficiency of any combustion engine depends particularly on the thermodynamic cycle of oneself. The exhaust gases produced during the operation of combustion engines contain a non-negligible proportion of thermal and kinetic energy in general.
By recovering the heat energy and feeding it into the combustion process increases the overall efficiency of the engine and at the same time reduces the fuel input required to generate power. Heat recovery systems (so-called recuperators) are used for this purpose. Recuperators extract part of the residual energy from the exhaust gas stream and refeed it into the machine process previous to combustion, so that less fuel is needed to achieve the necessary combustion temperatures.
This can be done by using the cross-flow, co-flow or counter-flow principle or a mix of these. Application areas of this technology are micro gas turbine based range extension systems or combined heat and power plants (CHP) as also aircraft engines in the future.
For this purpose, Euro-K GmbH offers solutions individually oriented to customer requirements.
Euro-K GmbH develops combustion systems for small energy converters based on micro turbines. Our systems are characterized as high reliability with low maintenance requirements.
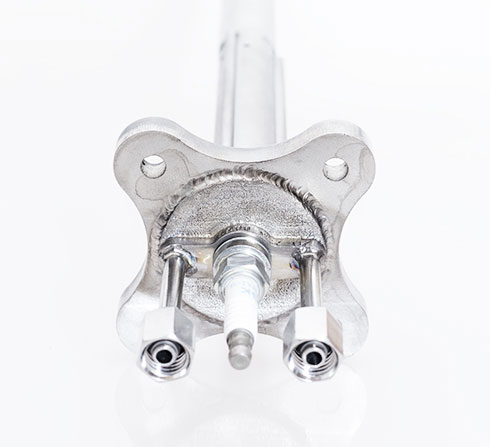
Efficiency and pollutant emissions play a crucial role here. The burner systems developed are characterized by a high burnout degree and the associated low emissions (partial zero emission). This means that future environmental regulations can be complied with and undercut. With suitable design concepts, the combustion systems with minor modifications are in the position to make use of both liquid and gaseous fuels. This leads to the fuel-flexibility, which can be customized to individual requirements depending on the existing infrastructure.
Currently available burner solutions can be operated with diesel, ethanol/fusel oil, natural gas, propane, butane, biogas, lean gas and mixed gas with a hydrogen content of up to 30 %. The systems are also characterized by high reliability with low maintenance requirements. The use of a wide variety of manufacturing processes, such as additive manufacturing, enables us to keep both acquisition and follow-up costs at a low level.
As an example, the ZB-100 ignition system already in use for the initial ignition of a 100 kW micro gas turbine is here to mention. Future developments of our combustion systems are aimed for the utilization of alternative fuels such as biomass or gases with a hydrogen content of more than 30 %.
The most vital innovation at present is the development and production of a micro turbine-based turbo range extender (TRE) for usage in commercial vehicles.
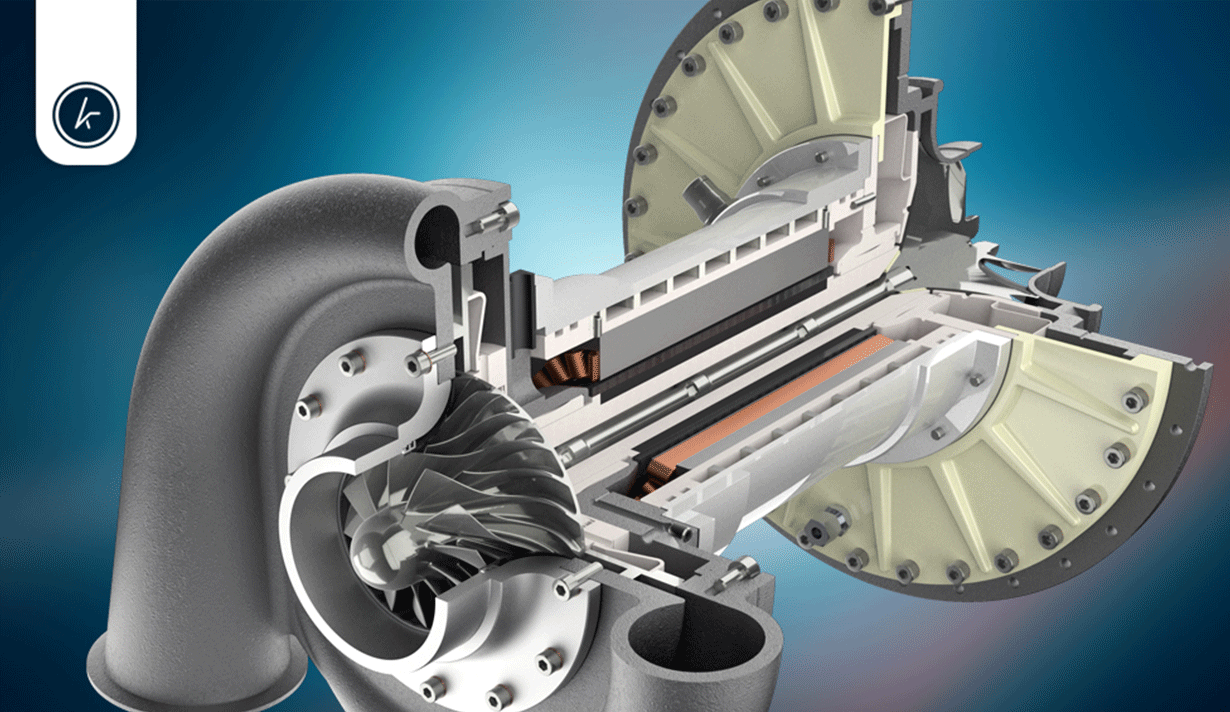
Under the background of declining resources, especially in regard to fossil fuels, and the growing environmental awareness accompanied with this, the technology to be developed has become increasingly important. In the context of electro mobility, the one topic, which becomes more and more aware in public focus, shows itself as, among other things, the possibility of reducing dependence on petroleum-based fuels. However, there are still restrictions with regard to the battery system and thus the range to be achieved. This is where the range extender concept of Euro-K GmbH comes into consideration. The range extender technology is considered as a transitional solution until the final large-scale introduction of “electric vehicles”.
So far, the batteries of electrically powered vehicles have too low an energy density to cover conventional driving profiles with ranges of more than 200 km. In order to make vehicles with extremely low-emission along driving more attractive for the mass market, optimized micro gas turbine systems are to be counted, which continuously actuate a generator and thus charge the batteries simultaneously, especially for the mobile range. Consequently, the range of the combined systems can be tremendously improved to 1,000 – 1,500 km range. The thermal converters used are no longer directly coupled to the powertrain (serial hybrid) and therefore run continuously at the design point. This leads to lower consumption, speed stability and permanently optimum load behavior, than that of the conventional actuation.
Euro-K GmbH has been using RP processes in economically demonstrated areas for a long time. These include development (e.g. burners for various fuels such as gases, powders and liquids), design space researches and the production of customer models as well as design studies. Especially in the development of functional components, whose behavior is often very time-consuming and cost-intensive to simulate, a significant number of designs can be tested directly by producing functional prototypes.
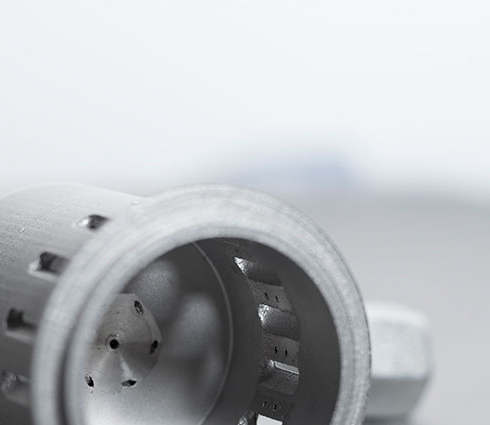
The results of these tests are used in parallel to validate the simulations and thus impressively improve the quality of subsequent numerical simulations, also in other projects. RP processes already used by Euro-K GmbH include Fused Deposition Modeling, Direct Light Processing-Stereolithography, Selective Laser Sintering or Selective Laser Melting.
The rules and boundary conditions to be considered for the respective process are taken into account and implemented by Euro-K GmbH through a production-oriented design, which significantly reduces the manufacturing costs for prototypes.
EURO-K | PURE GERMAN ENGINEERING
Tel.: +49 (0)30 120 596 40
Mail: service [at] euro-k.de